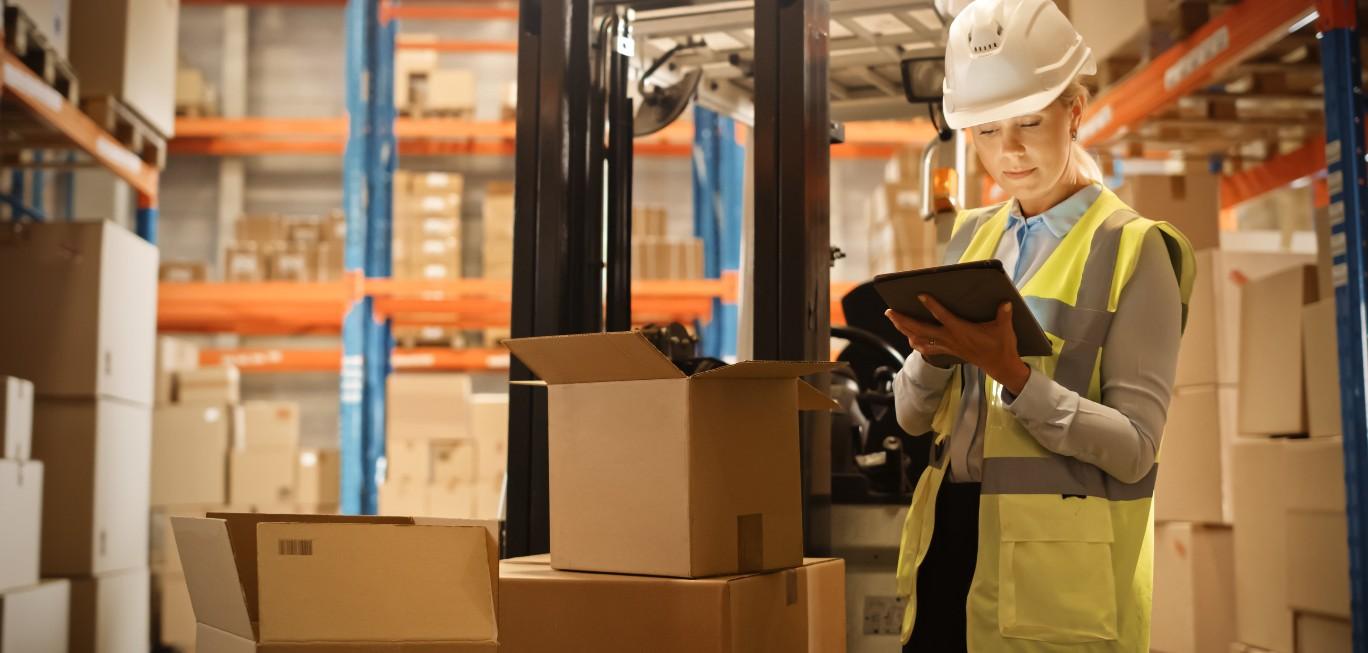
What is a Pre-shipment Inspection / Final Random Inspection?
A Pre-Shipment Inspection (PSI) or Final Random Inspection (FRI) is an inspection service that is conducted before shipment when your production is 100% completed and at least 80% packed.
Â
When should you use Pre-shipment Inspection / Final Random Inspection?
Before you ship. We suggest you reserve ample time for a Pre-Shipment Inspection (PSI) or Final Random Inspection (FRI) according to your shipment schedule. The time to reserve really depends on
-
the risk you can take if the inspection result is a fail.
-
the time factory needed to take corrective actions.
Â
Why should you use Pre-Shipment Inspection / Final Random Inspection?
A Pre-Shipment Inspection (PSI) or Final Random Inspection (FRI) is excellent insurance for your business and products before you ship. It is an effective inspection service to ensure the final products and packaging are in line with prescribed specifications. It safeguards your product against costly risks and helps you make an informed decision before releasing the shipment.
Â
How does it work?
A Pre-Shipment Inspection (PSI) or Final Random Inspection (FRI) will choose a specific quantity of completed products according to AQL. Our qualified inspectors help you assess whether the final product meets all quality specifications (i.e. color, workmanship, label, function, fit, packaging of products, etc.) according to your standard.
What is the Pre-Shipment Inspection / Final Random Inspection process?
- Get a consultation session with us or directly book via InSpec by BV
- Choose onsite inspection or remote inspection
- Submit your production specification or approved samples
- Our inspectors perform onsite or remote inspection
- Inspection Report ready for you
Â
Book Pre-shipment Inspection fast and easy with InSpec by Bureau Veritas
InSpec by BV is the go-to digital solution for product inspection, trusted by top brands and retailers. You can easily book product inspection online for your products and get world-class support from our team to ensure your inspection program is a success.
The benefits of using InSpec by BV:
- Global service coverage and customer support
Get world-class support from our on-the-ground global service team with over 1200 fully qualified specialists in over 85 countries across 5 continents. - World-leading expertise in quality control and quality assurance
Get support from our world-leading expertise and decades of experience assessing millions of products and factories for top brands and retailers worldwide. - Fast service delivery and reliability
Our inspection specialists can visit your factory the next working day in most Asian countries. You can get your inspection report on the same day of the inspection. It also allows you to cancel booking up to the day before the inspection. - Easy-to-use digital platform
Book your inspection and audit services online in just a few steps. Manage all your bookings and reports in one place. - Real-time quotation
View the inspection quotation online with no hidden cost.
Â
What products are commonly inspected by our clients?
There are a variety of products that are commonly inspected by our clients. These include but are not limited to the following:
- Electrical and Electronics
- Clothing
- Footwear
- Handbags and luggage
- Housewares
- Furniture
- Sports goods
- Outdoor products
- Toys
- and many more
Each product has its own distinct set of requirements that must be dealt with before launching to market. For example, electronic products will need to meet specific standards for safety and functionality, and clothing will need to meet quality and sizing standards. Infant products such as toys must be aware of small parts, sharp edges, etc. For comprehensive compliance, it may require lab testing.Â
Please feel free to contact us if you need support.
Which type of product inspection is best for me?
Your Key Challenges
Our Solutions
- My products are in their initial production process, and I want to verify their quality now to ensure:
- product quality consistency
- minimize the risks of wasted time, scrap products, rework, and shipping delays due to quality issues.
- I am working with a new supplier, new raw materials, and want to ensure quality requirements are met.
- I want to make sure everything starts right at the beginning.
- I want to reduce the product return rate and maintain profitability.
Initial Production Check
Learn More- My products are in the middle of a production process (usually 40%-60%).
- I want to ensure product quality and specifications are in line with quality requirements during the mass production stage.
- I want to avoid production delays that may be caused by quality and compliance issues.
- I want to reduce the product return rate and maintain profitability.
During Production Check
Learn More- The product production is completed, but I want to verify the quality requirements are met before shipment.Â
- I want to know the shipment's quality so I can make an informed decision about whether to accept the shipment. Also, to avoid disputes about product quality with my suppliers or clients.
- I want to have data and a quality report as a tool for continuous quality improvement.
- I want to reduce the product return rate and maintain profitability.
Pre-Shipment Inspection
Learn More​​​​​I need my products to be inspected one by one because:
- ensuring quality for each one of them is important.
- they are high-value items.
- every product return will impact my bottom line.
- every product return will impact my brand.
- I want to ensure every single customer is satisfied with my product.
Full Inspection
Learn More- I want to ensure the correct products and quantities are loaded before shipping to their destination.
- I want to ensure the containers being used are in optimal condition so the quality of my products will not be affected during transit.Â
Container Loading Supervision
Learn MoreI want to get an authentic sample, which is an accurate representation of mass production. I can use the sample for:
- Lab testing
- Act as a golden sample for inspection, and production etc.
- Keep it as my own sample reference.
- and more...
Sample Collection
Learn MoreInSpec By
Bureau Veritas
Bureau Veritas is a world-leading concept-to-consumer supply chain solutions partner working with organizations throughout the supply chain, With well in excess of 100 offices and laboratories spread around the world we are proud to be the quality managers for many of the world’s leading brands, retailers and their supply chains.
Inspec is an online booking platform to improve your product quality and reduce returns with systematic inspection and audits, You will experience a fast, easy-to-use booking flow for your product inspection services, and you can book one of our next available product specialists to be at your factory for service as quickly as the next day.
Why Bureau Veritas?
Bureau Veritas is a world leader in laboratory testing, inspection and certification services. Created in 1828, the Group has more than 80,000 employees located in more than 1,600 offices and laboratories around the globe.
As one of the world's leading third-party inspection companies, our inspection team all undergo rigorous technical qualification and integrity training before performing any type of inspection. We offer standard and tailor-made quality control inspection for a wide array of softline and hardline products.
Bureau Veritas helps its clients improve their performance by offering services and innovative solutions in order to ensure that their assets, products, infrastructure and processes meet standards and regulations in terms of quality, health and safety, environmental protection and social responsibility.
Global footprint and local expertise
Bureau Veritas carries out over 400,000 inspections and audits every year. We have over 1200 fully qualified inspectors across 85 countries in Asia, Africa, Europe, North and South America.
Product expertise
Your product quality inspection is conducted with BV’s inspection protocols which are based on our standard practices and decades of experience from assessing millions of factories and products. All our protocols are optimized to meet today’s requirements.
Ethic & independent quality control
As the world leader in testing, inspection and certification services, we put ethics and integrity at the very top of our priority list. Our Code of Ethics ensures our staff members maintain integrity, professional competence, confidentiality, professional behavior, and high ethical standards in their day-to-day business activities.