How we help you in the sourcing process.
Learn more about our services
Challenges
With decreasing product life cycles and time-to-market, the challenge to deliver quality products on-time increases. If a product does not meet the appropriate quality specifications for the marketplace – either after or late in the production stage – the result can be loss of product and revenues, delayed shipment or wasted materials, and the potential risk of increased returns.
Our solution
An inspection is the verification of product quality and quantity to pre-identified specifications before, during or after the production process. Inspections throughout the various stages of production can help both buyers and manufacturers monitor that quality requirements for the product are being met and support on-time delivery of quality products.
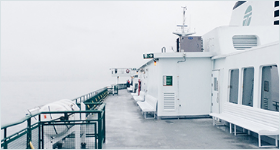
FROM $288
1-25% produced, typically performed at 10-20%. Not packed.
Why inspect?
Verifying first run quality requirements can help product consistency and minimize wasted time, scrap product, rework and shipping delays.
Typical Applications
High Risk Products (Toys)
New Factories
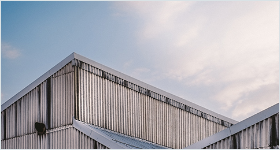
FROM $288
26-99% produced, typically performed at 40-50%. Not packed
If less than 26% is produced ,we will carry out an IPI as default
Why inspect?
Validates goods being produced continue to meet quality requirements.
Typical Applications
Medium Risk Products (E&E)
Poorly Performing Existing Factories
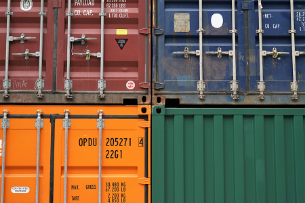
FROM $288
100% produced. 80% packed
If less than 100% is produced/80% packed, we will carry out a DUPRO/IPI as default
Why inspect?
Assess whether final product meets all quality specifications (i.e. color, workmanship, label, function, fit, packaging of product, etc.) and can be shipped without delay.
Typical Applications
All Shipments
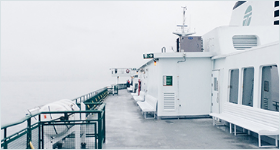
1-25% produced, typically performed at 10-20%. Not packed.
Why inspect?
Verifying first run quality requirements can help product consistency and minimize wasted time, scrap product, rework and shipping delays.
Typical Applications
High Risk Products (Toys)
New Factories
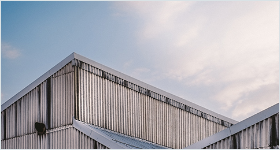
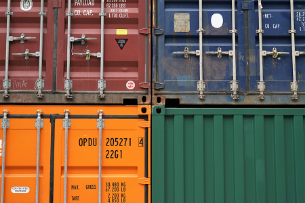
Why an inspection?
Cost Reduction
Reduce future costs including risk of rejects, charge backs and returns as well as recalls and brand/reputational damage.
Revenue Improvement
Prevent late shipment and stop paying for defective goods.
Quality Improvement / CX Alignment
By inspecting products prior to shipment, the risk of poor quality products being released to market is reduced. It also allows you to have a perspective of your customer's buying "experience" pre-shipment.
Process Improvement
Inspections are a source of data and manufacturing intelligence on how production processes are performing providing insights into how a better design might lead to higher quality and less waste.
Why InSpec by BV?
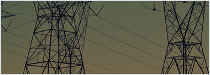
Geographical Coverage
Global network of full time trained specialists across 40 countries
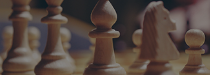
Product Specialists
Our inspectors, auditors and engineers know your products. We are specialized in consumer electrical and electronics, toys, hard goods and soft goods
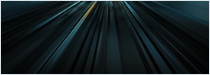
Speed
Industry leading turnaround times with next day inspection service for emergency shipments and late cancellations. Same day inspection reports available.
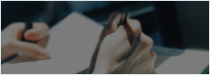
Service Excellence
Best in class technical governance controls the repeatability of our world class service globally
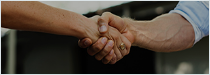
Client Aligned
Our Best Practice inspections and audits are based on decades of experience from assessing millions of factories with user friendly reports
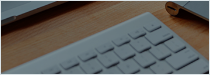
Always Informed
Our Platform provides notification alerts and supplier intelligence
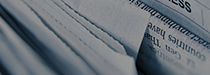
Continual Improvement
Access to Insight Center - improve your knowledge and quality sourcing